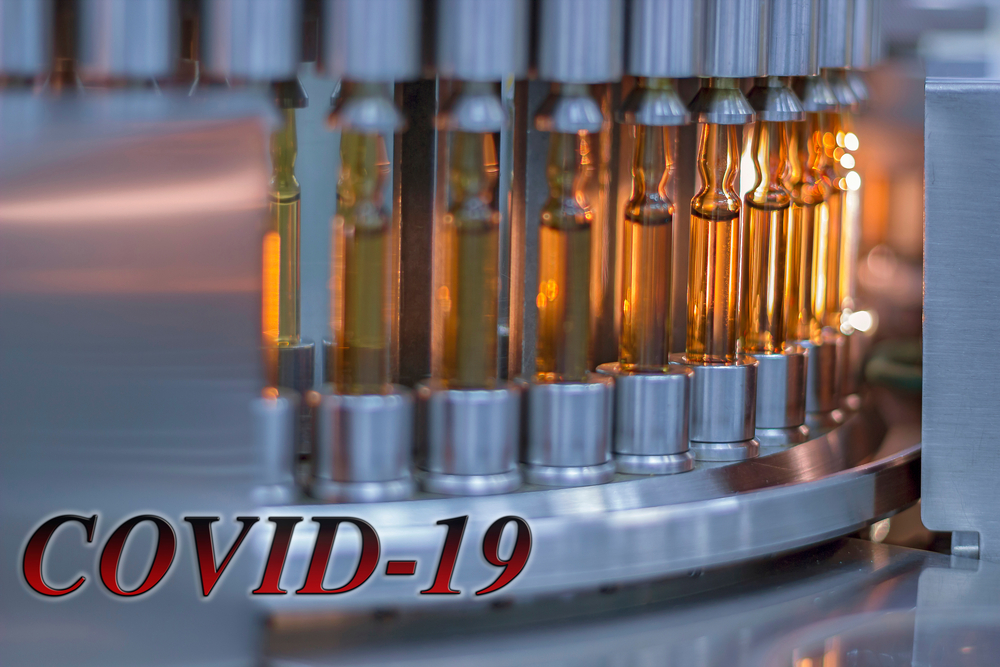
In the past few months, Covid-19 has presented a slew of serious challenges both human and business. From a business perspective, manufacturing industry is one of the most severely impacted. The spread of virus has resulted in plant closures (full or partial) in many countries, halting production for prolonged periods, resulting in huge losses and loss of jobs. The virus has highlighted various critical gaps in the manufacturing sector. Companies are building their business continuity plans and re-inventing new manufacturing supply chain models and exploring automation possibilities to reduce the impact of this crisis on production lines in the future.
Even prior to Covid-19, there was a steady rise in automation of industries, investments were growing at US$ 12 billion in 2017 to a projected US$ 60 billion in 2021. As of 2019, Europe has 106 industrial robots for every 10,000 workers, followed by 91 and 74 units in Americas and Asia. South Korea and Singapore have the highest density of robots, driven largely by the electronics industry, followed by Germany and Japan in the automotive sector. China, however, has seen the maximum growth in the last couple of years.
Contrary to popular belief that automation will replace manufacturing jobs, there has been a steady increase of automation in the manufacturing sector in India as well. The industry is expected to touch US$ 3.5 billion in 2020 creating 90 million jobs. Over the past few years, leading industry giants like L&T have digitally transformed 60% of their construction business by installing sensory equipment and gateways. Automakers like Mahindra have automated 70% of their body shop methods. Even the Indian Railways was able to reap 20% increase in efficiency by deploying MDCplus, a real-time machine monitoring and manufacturing data collection system developed by Zyfra, a Finnish-Russian digital solutions provider.
Companies like Cairn, an Indian oil and gas plant has shown that through automation and digitization, they were able to keep up their production of 1.6 lakh barrels of oil every day, as against 1.8 lakh barrels with less than 1/3rd of their workforce due to the quarantine measures.
While in the pre-crisis era, automation was viewed as a means to innovate, reduce cost and gain a competitive edge, now the purpose has shifted to survival and damage limitation. To mitigate global supply chain risks for future crises, manufacturers will consider bolstering their in-house capabilities instead of out-sourcing manufacturing to other countries. The pandemic will intensify the need to automate, especially in jobs that have high human interaction and the ones that are hazardous, causing death or injuries. Building technologies that will protect and provide workers and consumers, a safe environment will be the focal point in this drive to automate.
Although, the degree of adoption may be varied depending on the industry and the readiness of the companies to make huge investments at this time, the COVID-19 crisis has certainly acted as an catalyst to the transition to automation, specially in building resilience among businesses for future disruptions.
#Covid_19
- https://economictimes.indiatimes.com/news/economy/policy/india-russia-favour-digitalisation-to-mitigate-covid-impact-on-industry/articleshow/75065475.cms
- https://economictimes.indiatimes.com/news/company/corporate-trends/automation-key-to-post-pandemic-production/articleshow/75395665.cms?from=mdr
- https://www.weforum.org/agenda/2019/05/infographic-the-countries-with-the-highest-density-of-robot-workers