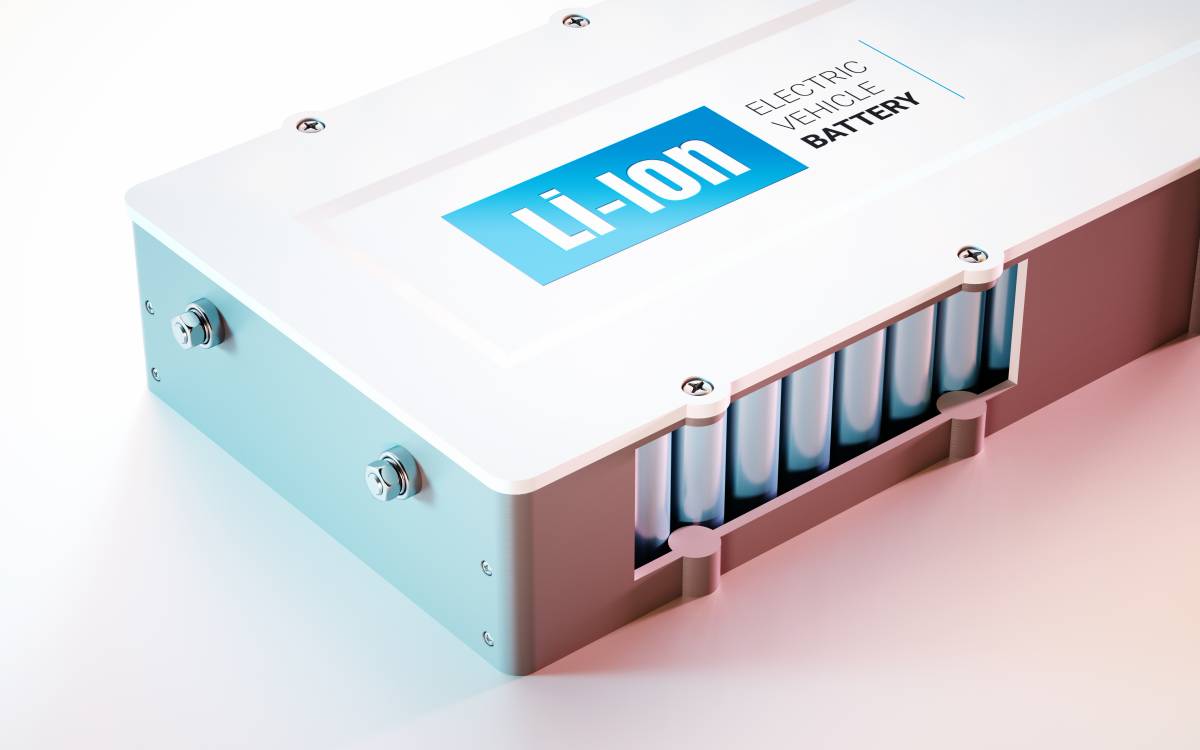
Lithium-Ion Batteries (LiBs) are getting popular in various applications like power tools and consumer electronics, not just electric vehicles. Climate change is real, and the automotive industry has taken cognizance of the changing consumer demand: electric vehicles. LiBs are considered a portable and elegant solution to power the electric vehicle.
Before we delve into the value chain, let's understand a bit about battery manufacturing. If LiBs play an essential role in electric vehicle technology, they play an equally important role in the cost structure. LiBs comprise almost 40% of the cost of an electric vehicle. Suppose you are a protagonist of electric vehicles. In that case, this cost is very crucial to understand as this cost structure can single-handedly decide the future of electric vehicles and thus, the possibility of a greener Earth.
65% of a battery cost is cell manufacturing. 35% is assembly. In the cost structure of cell, 35% is the cathode, 15% anode, 25% is the cell assembly, and 25% is the others like electrolyte and separators. The negative (anode) is cast mainly on the copper foil, whereas the positive (cathode) is cast on aluminum foil. A thin electron-insulating layer (aka separator) soaked with the electrolyte (liquid ion-conducting media) separates the two electrodes.
The Li-ion battery value chain consists of the four main stages, which include extraction and production of raw materials, cell component (electrodes) manufacturing, cell assembly, and, finally, recycling, which impact cost structure. This article will evaluate each stage of the value chain and look at challenges and their effect on the cost structure of a Lithium-Ion Battery.
Extraction and Production of Raw Materials
The raw material extraction stage plays a critical role within the value chain of Li-ion battery cells. The crucial factor in this stage is access to the appropriate mines.
Since extraction is not a core competency of automotive OEMs, they largely depend on metal and mining companies. The primary raw materials required for the cathode in cell manufacturing, which makes 35% of a cell cost and 10% of total EV cost, are Cobalt, Nickel, Lithium, and Manganese. Unfortunately, some of them are available in politically unstable regions.
Democratic Republic of Congo dominates over 60% of world’s Cobalt mining. The rising demand led to a 300% increase in Cobalt prices between 2016 and 2018. Lithium is controlled by 3 countries: Australia, Chile, and Argentina. Nickel supply is more fragmented: Brazil, Russia, South Africa, and Canada. But the challenge is that only “1st grade Nickel” is suitable for batteries, the availability of which, is limited.
From the analysis of the raw material stage of the LiB value chain, it can be concluded that the mining of certain critical materials is geographically localized. India faces a challenge: it lacks all the raw materials except graphite, which is used in anode (4% of EV cost).
Cell Components (electrodes) manufacturing
Cathode forms 35% of cell cost. Aluminium foil is used as a current collector for cathodes in Li-ion cells. Complex transition metal oxides and phosphates are currently the main cathode active materials used in Li-ion battery cells. These include Lithium Cobalt Oxide (LCO), Lithium Nickel Manganese Cobalt Oxide (NMC), Lithium Nickel Cobalt Aluminium Oxide (NCA), Lithium Manganese Oxide (LMO), and Lithium Iron Phosphate (LFP).
The global market for cathode materials, estimated at US$15 Billion in the year 2020, is projected to reach a revised size of US$22 Billion by 2027, growing at a CAGR of 5.6% over the analysis period 2020-2027. However, the potential of technological breakthrough that leads to the use of different cathode materials/chemistry, intensive competition, and government policy interference will continue to affect global cathode manufacturing sector.
Anode forms 15% of cell cost. Copper foil is used as a current collector for anodes in Li-ion cells. Various carbonaceous materials such as natural and artificial graphite, and amorphous carbon, and more recently Tin and silicon oxides and alloys, are used as anode active materials. The global lithium-ion battery anode market size is projected to grow from $ 8.4 billion in 2021 to $ 21.0 billion by 2026, at a CAGR of 19.9% from 2021 to 2026.
To be successful in this stage, players must force cost reduction to ensure competitiveness. This can be achieved through the improvement of all electrode manufacturing steps.
Cell Assembly
Cell assembly, following electrode manufacturing, is another complex process, consisting of several steps. It requires rigorous control of the production environment to avoid high moisture content in the finished cell. This is because traces of water can react with the electrolyte components, leading to rapid performance decay of the dead cells.
The global lithium-ion battery market is projected to grow from $ 41.1 billion in 2021 to $ 116.6 billion by 2030; it is expected to grow at a CAGR of 12.3% from 2021 to 2030. The growth of the lithium-ion battery market is majorly driven by the surging requirement for continuous power supply from critical infrastructures in the wake of COVID-19, increasing demand for plug-in vehicles, growing need for battery-operated material-handling equipment in industries due to automation, continued development of smart devices and growing adoption of lithium-ion batteries in the renewable energy sector.
China dominated the world's lithium-ion manufacturing market in 2020. That year, China produced some 77 per cent of all lithium-ion batteries that entered the global market. China’s success results from its large domestic battery demand, 72 GWh, and control of 80% of the world’s raw material refining, 77% of the world’s cell capacity, and 60% of the world’s component manufacturing, according to data from BNEF.
While China is projected to continue being the leading country in lithium-ion battery manufacturing in 2025, Europe is expected to significantly expand its production capacities. With planned investments into manufacturing facilities, Europe is poised to become the second-biggest producer of lithium-ion batteries in the world in 2025, accounting for around 25 per cent of the global production capacity.
Battery Cell Recycling
Undoubtedly, there will be a splurge in demand for lithium cells with the rising demand for electric vehicles. If current trends for handling these spent batteries hold, most of those batteries may end up in landfills even though Li-ion batteries can be recycled.
These popular power packs contain valuable metals and other materials that can be recovered, processed, and reused. The primary issue with lithium-ion recycling is that beyond smaller batteries used in consumer electronics, relatively few lithium-ion batteries (compared to lead-acid batteries) have reached the end-of-life stage because they haven’t been in the market all that long and they last a long time.
The lithium-ion battery recycling market is estimated at $ 1.5 billion in 2019 and projected to grow from $ 12.2 billion in 2025 to $ 18.1 billion by 2030, at a CAGR of 8.2% from 2025 to 2030. Rising investments in the development of electric vehicles are some of the key opportunities for the lithium-ion battery recycling market. Most companies have started recycling lithium-ion batteries as there is low accessibility for some raw materials such as lithium and cobalt.
Conclusion
Each part of the value chain must ensure that it plays a significant role in improving efficiencies and reducing costs. This will ultimately reduce the total cost of vehicle ownership, generating enough demand to bring economies of scale and further reducing prices. Thus, it becomes critical to break each aspect of the value chain and understand the impact on other ecosystem areas.
This blog is authored by Shikhar Goel.